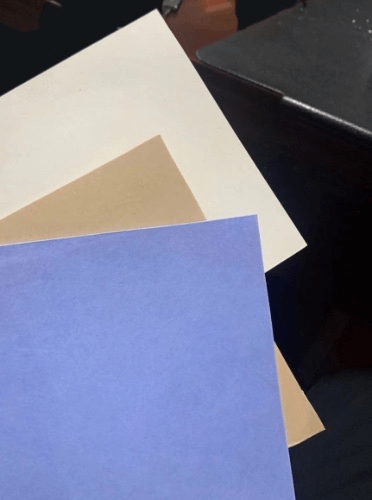
In order to improve the comprehensive performance of PTFE, people have been working hard on the modification of PTFE for many years. In the early days, the modification of PTFE mainly adopted the composite principle to combine it with other materials to form a PTFE composite material to make up for the defects of PTFE itself and improve its comprehensive performance. In the late 20th century, the wide application of PTFE promoted the development of polytetrafluoroethylene modification technology, and many new technologies were developed and applied.
Pure PTFE material properties
Pure polytetrafluoroethylene: white, commonly known as “non-stick coating” material, is a synthetic polymer material that uses fluorine to replace all hydrogen atoms in polyethylene. This material is resistant to acid and alkali, and various organic solvents, and is almost insoluble in all solvents. PTFE sheet is widely used as sealing seat of various flange gaskets and valves that need to resist acid, alkali and organic solvents. It has high lubricity, non-stickiness, electrical insulation, good anti-aging performance and excellent temperature resistance. (It can work for a long time at a temperature of 250°C to -180°C). PTFE itself is not toxic to humans and is allowed to be used in situations where the temperature is suddenly cooled and heated, or where the temperature is alternately operated.
From the above “pure PTFE material characteristics”, it seems that “pure PTFE material” is the most ideal material for flange gaskets of many medium pipes, but it is not. In the process of using pure PTFE sheets as seals, people discovered its biggest weakness, stress relaxation. “Pure PTFE board” has cold flow characteristics. “Cold flow” means that in a low temperature environment, the stress of the PTFE board will make its molecules slowly elongate and deform, and the molecules will flow. So it is called “cold flow”. In short, the gasket will gradually relax in stress in the sealed state, and finally the effect of permanent sealing cannot be achieved, so it is not suitable as a material for sealing gaskets.
The characteristics of modified PTFE materials
Modified filled PTFE is generally a sealing product made by adding a certain amount of fillers to PTFE resin, mixing uniformly at high speed, molding, and sintering at high temperature. Commonly used additives are: glass fiber, bronze powder, molybdenum disulfide, graphite, carbon fiber, etc.
Compared with “modified PTFE material” and “pure PTFE material”, the biggest advantage is that the polytetrafluoroethylene molecules are stabilized by adding glass fibers or glass beads during its production process, so that it can be used in routine There is no “cold flow” in the process, and it maintains high resilience and anti-cold flow characteristics. In terms of quality and technical indicators, the modified PTFE sheet is mainly reflected in the obvious decrease in density, and the quality indicators such as resilience, creep relaxation, and compression rate are significantly better than pure PTFE sheets. The processed modified PTFE sheet can choose to add some color-changing additives to make it different from the white color of pure PTFE material to prevent confusion in use.
Modified filled PTFE has excellent properties such as low friction coefficient, good compressive strength and wear resistance. This makes its use effect greatly exceed that of traditional PTFE, which not only improves the environment but also saves costs. Often used in industries such as chemical, petrochemical, hydrocarbon reaction and power plants.