Why Does PTFE Fill Some Materials?
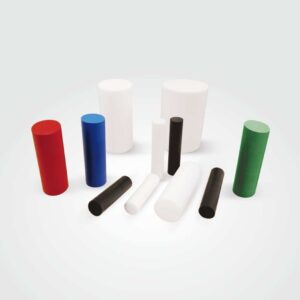
Filled PTFE (Modified PTFE) products are made of filled polytetrafluoroethylene resin by molding. Suspension polytetrafluoroethylene resin and a variety of fillers mixed into filled polytetrafluoroethylene resin. Fiberglass, carbon fiber, tin bronze and lubricants (such as graphite, molybdenum disulfide) are among the various fillers suitable for mixing with PTFE and have been widely used in large-scale production. Compared with pure PTFE, packed PTFE has the advantages of higher compressive strength, wear resistance, good thermal conductivity and reduced thermal expansion.
Virgin PTFE is capable in its own right, but when fillers are added, it enhances the material wear and deformation characteristics to more fully exploit their unique combination of chemical, physical and electrical properties.
PTFE materials become brittle at temperatures below -185 °C and creep cracking above 260 °C, so should not be used at excessive temperatures. PTFE products with low thermal conductivity and large linear expansion coefficient will have cold flow phenomenon under load, adding different fillers such as glass fiber, graphite, molybdenum disulfide, bronze powder can improve the performance of PTFE products.
Modified PTFE products using industries: Chemical, Petrochemical, Refining, Alkali, Acid, Phosphate Fertilizer, Pharmaceutical, Pesticide, Chemical Fiber, Dye, Coking, Coal Gas, Organic Synthesis, Non-ferrous Smelting, Steel, Atomic Energy and High Purity Products (e.g., ionic membrane electrolysis), viscous material transportation and operation, highly strict health food, beverages and other production departments.
Use equipment: pipe, valve, pump, pressure vessel, heat exchanger, condenser, generator, air compressor, exhaust pipe, refrigerator and other flange joint sealing parts.
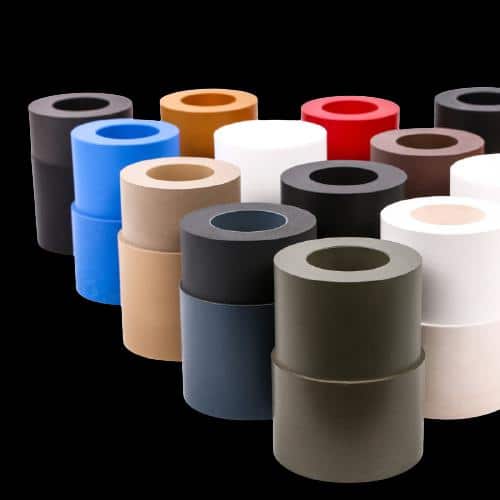